
Vibration Limits – Steam Turbines
If you operate turbomachinery you should be aware of the important vibration limits applicable to your machinery. There are a lot of standards for steam turbine vibration, and their specifications for measurement and evaluation are extensive and not easy to understand. However, a few essential guidelines can help you evaluate the vibration severity and, ultimately, enable you to decide on whether to investigate any faults.
Generally, a machine’s level of vibration is classified into one of four evaluation categories. These categories give you an indication of the severity of the vibration and the likelihood of damage occurring. These categories are as follows:
A
The vibration of machines newly comissioned normally falls in this zone
B
Acceptable for unrestricted long-term operation
C
Unsatisfactory for long-term operation
D
Sufficient severity to cause damage to the machine
The exact vibration limits for each of these vibration evaluation zones are given below. The limits depend on the machine size, the speed of rotation and the type of vibration being measured.

Examples:
-
For example, a 10 MW steam turbine with flexible foundation and bearing vibration of 4 mm/srms would be classified in zone B (small turbine, zone B is all values between 3.5 – 7.1 mm/srms ) and would therefore be considered “Acceptable for unrestricted long-term operation”.
-
Alternatively, a 50 MW steam turbine rotating at 3000 rpm with shaft vibration of 200 µmp-p would be classified in zone C (large steam turbine 40+ MW, zone C is all values between 165 µmp-p and 240 µmp-p) and would therefore be considered ”Unsatisfactory for long-term continuous operation”.
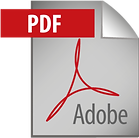
(1) General Notes: - Bearing vibration is evaluated as r.m.s vibration in mm/srms only (also known as “overall” or “effective” vibration). The frequency range of measurement is 10 Hz to 1,000 Hz. The direction of measurement is radial, and the location of measurement is on bearing pedestals/housings. The transducers may be placed at any angular location, although usually one sensor each in the vertical and horizontal directions are preferred. It is not common practice to measure axial vibration on main radial load-carrying bearings during continuous operational monitoring. However, in some cases the limits can be applied to axial vibration when measured on a thrust bearing with axial vibration correlating to the axial pulsations which could cause damage to the axial load-carrying surfaces.
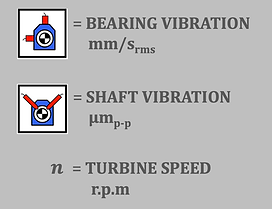